American Chemistry Council Conversion Technology: A Complement to Plastics Recycling
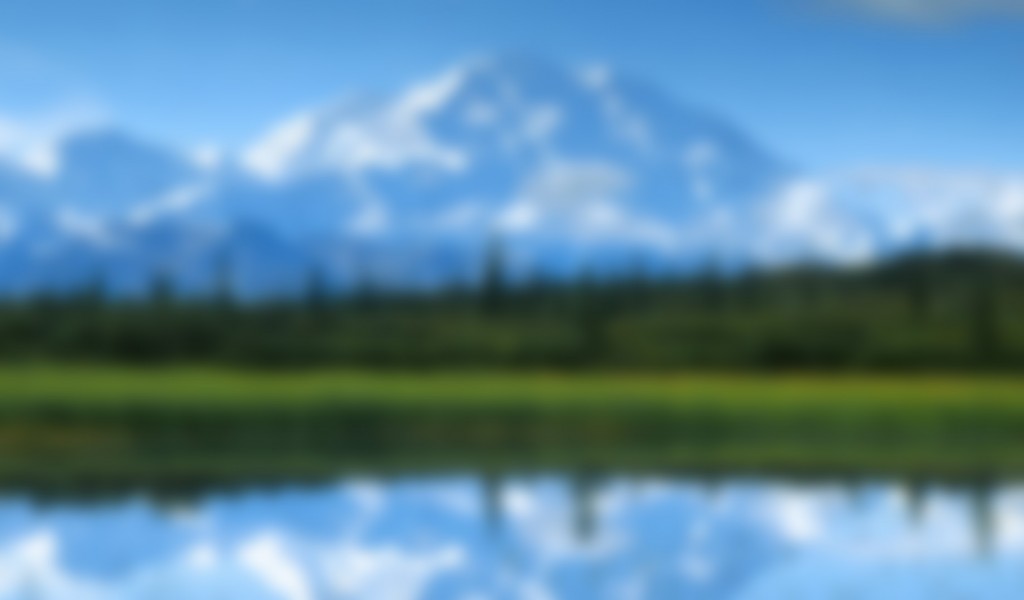
WASHINGTON, D.C. — Today the American Chemistry Council released a study conducted by 4R Sustainability, Inc. on increasing opportunities for plastics-to-fuel “conversion technologies” in the Unites States. Although in the United States plastics are made primarily from natural gas, these innovative technologies are effectively turning non-recycled plastics into crude oil and other fuels, helping to create a reliable source of alternative energy from an abundant, no-cost feedstock, and diverting this potentially valuable material from landfills. Many of these technologies are already being implemented on a commercial scale in Europe and Asia.
In 2009, the United States recycled over 4 billion pounds of plastics. This report demonstrates that we have an ability to recycle and recover more plastics through innovative technologies including those that allow us to convert plastics into oil and other fuels.
“As the United States seeks cost-effective sources of alternative energy, the potential to recover non-recycled plastics is enormous,” said Steve Russell, vice president of plastics for the American Chemistry Council. “According to scientists at Columbia University, if the United States were to recover the energy from our non-recycled plastics, this material could be converted into enough energy to fuel the equivalent of 6 million cars annually.”
The American Chemistry Council funded the study, “Conversion Technology: A Complement to Plastics Recycling“, to examine available technologies, feedstocks, growth models for technology abroad and in North America, opportunities and barriers, and outlook for growth in the United States. The information presented is intended to help inform government officials, plastics reclaimers, materials recovery facility managers, and investors about the range of available technologies and under what conditions each could fit in commercial or community waste management plans.
Consistent with the U.S. Environmental Protection Agency’s waste management hierarchy—reduce, reuse, recycle, recover—plastics-to-fuel technologies do not compete with recyclers for material. Rather, they tend to make use of non-recycled plastics—and in many cases run more efficiently with non-recycled plastics—which they convert into crude oil and other types of fuels.
Energy Recovery
Energy recovery is the process by which municipal solid waste is converted into feedstock materials or renewable energy. Energy recovery is happening right now, powering homes and businesses, and it’s helping to address our growing population’s biggest challenges: energy independence, waste diversion, and climate change.
Did you know…?
- The United States currently processes 13 percent of its solid waste, recovering enough energy to power homes in five states or the equivalent of 28.6 billion barrels of crude oil.
- Energy recovery facilities mean a lot less waste goes to landfills. Energy recovery facilities can reduce by 90 percent the volume of waste that goes to landfill.
- Modern energy recovery facilities are greener than ever, with fewer emissions. Today’s technology allows modern energy recovery facilities to process waste with fewer emissions than conventional fuels processed in most power plants. In fact, EPA estimates that energy recovery technology in use today helps prevent the release of 33 million metric tons of carbon dioxide annually.
- Plastics are high value “captured energy.” Plastics have significantly more captured energy than wood, paper or even coal.
- Plastics help energy recovery technology work better. Because plastics have a higher energy value than other components of municipal solid waste, they help to significantly increase the efficiency of the energy recovery process.